
在新冠疫情影響下,氣候變化和溫室氣體減排問題更加突出,各國政府進(jìn)一步加大“脫碳”力度,殼牌、BP、中石化等傳統(tǒng)能源企業(yè)已經(jīng)開始重組。其中,氫能是一種轉(zhuǎn)型的重要方向。氫能作為一種高效、清潔、可持續(xù)的能源,被視為21世紀(jì)最具發(fā)展?jié)摿Φ摹敖K極能源”。隨著我國碳達(dá)峰和碳中和目標(biāo)的出臺以及實(shí)現(xiàn)30/60目標(biāo)的政策實(shí)施,氫能將有更大的發(fā)展空間。預(yù)計(jì)未來10至20年,清潔氫在可持續(xù)能源中將逐漸發(fā)揮越來越重要的作用,并逐漸出現(xiàn)在各種能源消費(fèi)的比重中,為工業(yè)和交通領(lǐng)域的碳減排做出更重要的貢獻(xiàn)。在國家政策的鼓勵(lì)和企業(yè)的積極參與下,氫能源呈現(xiàn)出爆發(fā)式的發(fā)展。正從工業(yè)化初期過渡到快速發(fā)展期。但是,在這個(gè)過程中仍然存在很多問題。其中,氫氣的高成本是現(xiàn)階段的產(chǎn)業(yè)化階段核心問題。下面從制氫-儲氫-加氫產(chǎn)業(yè)鏈的角度分析氫氣成本。
1、制氫成本分析
1.1 天然氣和煤制氫成本分析
我國擁有豐富的氫氣資源,2020年我國氫氣產(chǎn)能約4100萬噸,產(chǎn)量約3343萬噸。中國已成為全球最大的氫生產(chǎn)國。由于我國氫燃料電池汽車數(shù)量較少,用作動力源的氫并不多。氫氣主要用于合成氨、煉油、甲醇生產(chǎn)、費(fèi)托合成等化工原料。目前,我國的制氫方式主要有煤制氫、天然氣制氫、水電解制氫、工業(yè)副產(chǎn)氫等。天然氣制氫主要是通過甲烷蒸汽重整,在催化劑的作用下產(chǎn)生H2和CO。分離后,CO被轉(zhuǎn)化并與水蒸氣反應(yīng)生成CO2和H2。天然氣水蒸氣重整制氫是一種技術(shù)成熟的傳統(tǒng)制氫工藝,廣泛用于煉油廠制氫、純氫、合成氣和合成氨原料,它是工業(yè)上最常用的制氫方法。
煤制氫主要以水煤漿或煤粉的形式,在氣化爐中在1000℃以上的高溫下與氣化劑(蒸汽/氧氣)反應(yīng)生成合成氣(H2+CO)、CO和H2分離后,CO通過水蒸汽轉(zhuǎn)化為H2和CO2,再經(jīng)過脫酸性氣體(CO2+SO2)和氫氣PSA提純,得到高純度氫氣。近年來,從原料的可獲得性和成本的角度來看,越來越多的煉油廠、尿素廠等制氫企業(yè)選擇煤制氫工藝。近年來,煤制油、煤制烯烴等煤化工行業(yè)的飛速發(fā)展,也為煤氣化技術(shù)提供了更大的發(fā)展空間,技術(shù)研發(fā)、工程設(shè)計(jì)和運(yùn)行水平不斷提高。
根據(jù)相關(guān)行業(yè)氫氣成本模型的計(jì)算方法,計(jì)算天然氣生產(chǎn)和煤炭生產(chǎn)的氫氣成本,結(jié)果如表1所示。
以上計(jì)算以原料天然氣價(jià)格2.5元/Nm3、煤炭800元/噸計(jì)算,同時(shí)對外銷售價(jià)格按毛利15%計(jì)算。通過以上靜態(tài)調(diào)查可以看出,天然氣成本占天然氣制氫成本的73%以上,煤炭成本占煤炭制氫成本的54%以上。相對而言,天然氣制氫對原材料價(jià)格更為敏感。圖1顯示了動態(tài)條件下相同氫氣成本與天然氣和煤炭價(jià)格的比較。由于我國天然氣價(jià)格主要由政府定價(jià),煤炭價(jià)格市場化,天然氣價(jià)格相對固定,波動不大。但煤炭價(jià)格受國家政策和市場供需影響較大,短期內(nèi)往往會出現(xiàn)大幅波動。煤制氫成本往往會相應(yīng)波動。因此,雖然煤制氫成本普遍低于天然氣制氫,但當(dāng)市場發(fā)生劇烈變化時(shí),其成本可能會超過天然氣制氫。
無論是天然氣制氫還是煤制氫,在生產(chǎn)過程中都會產(chǎn)生二氧化碳,即產(chǎn)生的氫屬于“灰氫”。在雙碳目標(biāo)下,通過碳捕獲(CCUS)技術(shù)生產(chǎn)的“藍(lán)氫”是未來的方向。但由于CCUS技術(shù)不成熟,除國內(nèi)少數(shù)示范項(xiàng)目外,尚未得到廣泛推廣。在目前的技術(shù)水平下,用CCUS疊加天然氣制氫將使氫氣成本增加33%。由于煤制氫的碳排放強(qiáng)度高于天然氣,因此疊加CCUS后,煤制氫的成本將增加近50%。如果征收碳稅,在175元/t CO2的條件下,天然氣制氫成本將增加0.84元/kg,煤制氫成本將增加3.85元/kgH2??紤]到碳排放成本,如果未來原材料價(jià)格不顯著,天然氣制氫成本可能低于煤炭制氫成本。顯然,在氫能發(fā)展的初期,在氫的成本還比較高的時(shí)候,CCUS和碳稅的推廣不利于氫能的快速推廣。
1.2 電解水制氫成本分析
電解水是一種操作靈活的綠色環(huán)保制氫方法,該產(chǎn)品純度高,技術(shù)相對成熟,可與風(fēng)電、光伏等可再生能源耦合制氫,實(shí)現(xiàn)規(guī)?;茪?。在現(xiàn)有技術(shù)條件下,電解水作為綠色制氫的主要方式,近年來受到市場的青睞,制氫規(guī)模也逐漸從兆瓦級向千兆瓦級邁進(jìn)。根據(jù)電解液的不同,目前水電解技術(shù)分為堿性電解水(AWE)、質(zhì)子交換膜電解水(PEM)和固體氧化物電解水(SOEC)三種。三種電解水技術(shù)的比較見表2。
堿水電解制氫技術(shù)產(chǎn)業(yè)化時(shí)間較長,技術(shù)最為成熟,具有投資成本低、操作簡單、使用壽命長等優(yōu)點(diǎn),但能量轉(zhuǎn)換效率低,產(chǎn)氣需脫堿;質(zhì)子交換膜電解槽原理與堿性電解槽不同。固體質(zhì)子交換膜取代了傳統(tǒng)AWE技術(shù)中的液體電解質(zhì)和隔膜,具有無污染、結(jié)構(gòu)致密、體積小等優(yōu)點(diǎn),能快速改變負(fù)載,響應(yīng)時(shí)間短,與光伏、風(fēng)電(發(fā)電的隨機(jī)性和波動性)匹配性好。雖然目前受制于膜電極的高成本,但該技術(shù)被廣泛看好,是目前研發(fā)的主要方向;固體氧化物電解槽由于工作溫度高,材料選擇有限,尚未商業(yè)化。
為估算水電解制氫成本,參照相關(guān)計(jì)算方法,作如下假設(shè):
(1)采用堿性電解池制氫,制氫規(guī)模1000Nm3/h,年產(chǎn)氫200萬Nm3;
(2)設(shè)備投資1000萬元,土建、安裝調(diào)試等費(fèi)用300萬元,總投資1300萬元,10年折舊,年工時(shí)2000小時(shí),采用直線折舊法,無殘值;
(3)光伏電站供電,1Nm3制氫電耗5kWh,電價(jià)0.3元/kWh;
(4)維修費(fèi)用(含人員工資)60萬元;
(5) 毛利15%。
從表3可以看出,電費(fèi)占電解水氫氣成本的60%以上,其余為固定成本。需要注意的是,本次調(diào)查采用0.3元/千瓦時(shí)計(jì)算基準(zhǔn),電價(jià)偏低。如果采用正常的上網(wǎng)電價(jià),氫的成本會更高,電費(fèi)也將占成本的更大比例。電解水制氫要達(dá)到與化石能源制氫同等的價(jià)格競爭力,需要將電價(jià)降到0.05元以下,這在近期很難實(shí)現(xiàn)。結(jié)合表1和表3可以看出,雖然目前各國都在大力發(fā)展電解水制氫,但在30/60政策目標(biāo)的引導(dǎo)下,“綠色氫”也受到越來越多的關(guān)注,但在當(dāng)前價(jià)格水平,電解水制氫成本遠(yuǎn)高于化石能源。因此,在當(dāng)前的氫能市場推廣期,要依靠低成本的“灰氫”資源。
1.3 工業(yè)副產(chǎn)氫成本分析
工業(yè)副產(chǎn)氫是指工業(yè)過程中產(chǎn)生的氫氣不是目標(biāo)產(chǎn)品,而是副產(chǎn)品,主要包括煉油廠催化重整、丙烷脫氫、焦?fàn)t煤氣和氯堿化學(xué)品等。本部分副產(chǎn)氫氣產(chǎn)量大,對氫燃料電池汽車產(chǎn)業(yè)的發(fā)展具有巨大的回收利用潛力,每種副產(chǎn)氫的產(chǎn)品性質(zhì)和成本見表4。
雖然我國工業(yè)副產(chǎn)氫資源豐富,在工業(yè)發(fā)展初期可以起到助推器的作用,但氫能產(chǎn)業(yè)的長遠(yuǎn)發(fā)展不能完全依賴副產(chǎn)氫。究其原因,一方面是副產(chǎn)氫資源分布不均。例如,副產(chǎn)氫資源最多的焦炭行業(yè)與我國煤炭產(chǎn)區(qū)高度重疊,基本分布在西北地區(qū)。幾乎所有的丙烷脫氫項(xiàng)目都位于沿海地區(qū)。不能覆蓋全國;另一方面,隨著近年來我國環(huán)保節(jié)能要求的提高,企業(yè)的精細(xì)化管理水平也有所提高。焦化企業(yè)利用焦?fàn)t煤氣生產(chǎn)甲醇、合成氨、LNG 或煤焦油加氫,氯堿工業(yè)利用副產(chǎn)氫生產(chǎn)鹽酸或聚氯乙烯,實(shí)際可利用的副產(chǎn)氫不及大如預(yù)期。因此,副產(chǎn)氫只能作為發(fā)展氫能的部分補(bǔ)充,不能完全支撐我國未來的氫能產(chǎn)業(yè)。
2 氫運(yùn)輸成本分析
目前,氫輸運(yùn)方式主要有高壓氣氫、低溫液態(tài)氫和管道輸氫三種。其中,高壓氣氫運(yùn)輸是目前主流的運(yùn)輸方式,高壓氫氣運(yùn)輸是通過壓縮機(jī)將高壓氫氣(工作壓力10~30MPa,通常為20MPa)儲存在壓力容器中,用長管拖車運(yùn)輸,長管拖車的壓力容器通常由6-10個(gè)大容積無縫高壓鋼瓶組成。這種方法目前已經(jīng)成熟,應(yīng)用廣泛。但由于氫氣密度低,儲氫壓力容器較重,拖車運(yùn)輸?shù)臍錃赓|(zhì)量僅占總運(yùn)輸質(zhì)量的1%~2%。這是每輛車常見的國內(nèi)氫運(yùn)輸量,約260~460kg。另外,氫氣瓶卸車時(shí)間長,約需2~6小時(shí),效率低。
液氫輸送是將氫氣深度冷凍至21K液化,然后通過0.6MPa的特制低溫保溫罐輸送。由于液氫密度達(dá)到71g/L,液氫罐車容量約為65m3,每次可運(yùn)輸約4000kg氫氣,是氣氫拖車運(yùn)輸量的10倍以上,這大大提高了運(yùn)輸效率,適用于大規(guī)模、長距離運(yùn)輸,但這種方法的缺點(diǎn)是生產(chǎn)液氫消耗大量能量(總能量的30%~40%用于液化),并且在液氫的儲存和運(yùn)輸過程中會發(fā)生一定的蒸發(fā)損失,需要在終端建設(shè)特殊的接收設(shè)施抬高成本。此外,由于我國關(guān)鍵液氫設(shè)備(如透平膨脹機(jī)、3000立方米以上大型液氫儲罐、液氫泵等)與發(fā)達(dá)國家差距較大,仍很大程度上依賴進(jìn)口,它還不能成為氫儲存和運(yùn)輸?shù)闹饕侄巍?/span>
管道氫氣運(yùn)輸是實(shí)現(xiàn)氫氣大規(guī)模、長距離、低成本運(yùn)輸?shù)闹匾緩?。目前,全球有?000公里的氫氣管道,而中國只有不到100公里。由于管材存在“氫脆”現(xiàn)象,氫氣管道需要采用低碳鋼,需要特殊處理,導(dǎo)致成本是普通天然氣管道的兩倍以上。因此,成本是制約氫氣管道建設(shè)的重要因素。目前的研究熱點(diǎn)是利用現(xiàn)有的天然氣管網(wǎng)混合輸送氫氣。據(jù)研究,如果混合氫氣控制在15%~20%,可直接利用現(xiàn)有天然氣管道輸送。德國和英國也建立了類似的示范項(xiàng)目。如果成功驗(yàn)證氫氣混合路線,解決氫氣和天然氣管道的兼容性問題,西部地區(qū)可以利用自身在光伏和風(fēng)能方面的優(yōu)勢生產(chǎn)氫氣,充分利用現(xiàn)有的天然氣主管道和支線網(wǎng)絡(luò)進(jìn)行西氣東輸,將氫氣遠(yuǎn)距離運(yùn)輸?shù)綎|部地區(qū),大大降低了氫氣運(yùn)輸成本。目前,該研究僅處于實(shí)驗(yàn)階段,面臨分離等技術(shù)難點(diǎn)。因此,管道氫運(yùn)輸短期內(nèi)不具備成為氫運(yùn)輸主要方式的可能性。
除上述三種方法外,還有利用化合物儲氫等方法,常用的儲氫材料有環(huán)己烷、咔唑、十氫化萘、液氨、甲醇、氫化鎂、氫氧化鎳等,但仍在試驗(yàn)中。在實(shí)驗(yàn)室研究階段,暫時(shí)沒有推廣的可行性。
可以看出,未來中短期內(nèi)高壓氣氫仍將是輸送氫氣的主要方式,因此本文主要以高壓氣氫來考察氫氣的成本。受國內(nèi)標(biāo)準(zhǔn)約束,目前長管拖車的最大工作壓力限制在20MPa,每次氫氣質(zhì)量小于500kg,但國際上已經(jīng)引進(jìn)了50兆帕氫氣長管拖車,每次可運(yùn)輸1000~1500公斤氫氣。如果放寬國內(nèi)儲運(yùn)壓力標(biāo)準(zhǔn),同樣體積的管束可以含有更多的氫氣,從而降低運(yùn)輸成本,因此也研究了50MPa壓力下的運(yùn)輸成本。
為計(jì)算方便,作如下假設(shè):
(1)長管拖車滿氫質(zhì)量為350kg(20MPa)/1200kg(50MPa),管束內(nèi)氫殘留率為20%;
(2)氫源距加氫站100km,加氫站每天使用氫氣500kg;
(3)拖車百公里油耗25L,柴油價(jià)格6.5元/L;
(4)拖車車頭與管束70萬元,折舊10年,折舊方法為直線法;
(5)每輛車配備一名司機(jī)和一名裝卸操作員,人員費(fèi)用10萬元/年,車險(xiǎn)費(fèi)用1萬元/年,維修費(fèi)用0.3元/公里,過路費(fèi)0.6元/公里;
(6)每個(gè)氫氣壓縮過程耗電1kWh/kg,電價(jià)0.6元/kWh;
(7) 氫運(yùn)輸毛利為15%。
運(yùn)輸距離為50km時(shí),氫氣運(yùn)輸成本為4.9元/kg;隨著運(yùn)輸距離的增加,長管拖車的運(yùn)輸成本逐漸上升,當(dāng)運(yùn)輸距離為500km時(shí),運(yùn)輸成本接近22元/kg,所以要考慮經(jīng)濟(jì)問題,長管拖車一般適用于200km以內(nèi)距離較短、運(yùn)輸量較小的運(yùn)輸場景。另外可以看出,隨著距離的增加,20MPa和50MPa運(yùn)輸條件下的成本逐漸分化,50MPa下的成本優(yōu)勢越來越明顯。運(yùn)輸距離為200km時(shí),成本差約為4元/kg。因此,從經(jīng)濟(jì)角度來看,提高鋼瓶儲氫壓力勢在必行,這將是未來高壓氫氣運(yùn)輸?shù)陌l(fā)展方向。
3 加氫站加氫成本分析
加氫站是保障燃料電池汽車運(yùn)行的重要基礎(chǔ)設(shè)施。作為整個(gè)氫氣供應(yīng)鏈的終端,其成本也應(yīng)計(jì)入氫氣成本。典型的加氫站由壓縮系統(tǒng)、存儲系統(tǒng)、加氫系統(tǒng)和控制系統(tǒng)組成。從站外長管拖車運(yùn)來的氫氣通過壓縮系統(tǒng)壓縮到一定壓力,加壓后的氫氣儲存在固定的高壓容器中。當(dāng)需要加氫時(shí),在加氫站固定高壓容器與車載氫氣之間的高壓差作用下,通過加氫系統(tǒng)將氫氣快速填充到車載儲氫罐中儲存容器。除了土建成本和管道閥門,加氫站成本的主要部分是核心設(shè)備,如壓縮機(jī)、加注設(shè)備和儲氫罐。由于國內(nèi)缺乏成熟、量產(chǎn)的加氫站設(shè)備制造商,進(jìn)口設(shè)備推高了加氫站的建設(shè)成本,為了計(jì)算加氫站的單位氫氣成本,做出以下假設(shè):
(1)加氫站日加氫能力500kg,全年365天運(yùn)營,設(shè)備采購安裝費(fèi)1200萬元,土地及土建費(fèi)300萬元,固定成本共計(jì)1500萬元。
(2)設(shè)備折舊15年,土地房屋折舊30年,采用直線法折舊,無殘值;
(3)管理、維護(hù)、人工費(fèi)用200萬元/年;
(4) 毛利20%。
從表5可以看出,加氫站仍占?xì)錃獬杀镜暮艽蟊壤?。一方面,氫氣的性質(zhì)使得加氫站比傳統(tǒng)加油站更加復(fù)雜。同時(shí),關(guān)鍵設(shè)備對進(jìn)口的依賴導(dǎo)致初期投資較高。目前氫燃料電池汽車數(shù)量較少,每日加氫量有限,導(dǎo)致折舊及攤銷成本較高。如果加氫量增加一倍,單位加氫成本可以增加一倍,大大降低了灌裝過程的成本。
基于以上分析,計(jì)算了整個(gè)產(chǎn)業(yè)鏈的制氫成本,計(jì)算結(jié)果如表6所示。同時(shí),以天然氣制氫為例,不同部分的成本占比考察了20MPa條件下不同運(yùn)輸距離的氫氣,結(jié)果如圖3所示。
從表 6 和圖 3 可以看出,目前氫氣成本居高不下的原因是運(yùn)輸和加氫成本占比過高,占總成本的 60% 以上,遠(yuǎn)高于傳統(tǒng)成品油產(chǎn)業(yè)鏈相應(yīng)環(huán)節(jié)。與電動汽車和燃料汽車相比,氫燃料電池汽車的能源成本普遍較高,仍需進(jìn)一步降低成本。
4 降低氫氣成本的建議
綜上所述,要想盡快推廣氫燃料電池汽車,必須進(jìn)一步壓縮氫的成本,降低汽車使用氫的負(fù)擔(dān)。提出以下建議:
(1)降低可再生能源電價(jià),大力發(fā)展水電解制氫。從以上價(jià)格對比可以看出,電費(fèi)需要降低到0.05元以下,這樣電解水制氫成本才能與化石能源制氫成本競爭。與化石能源制氫成本相比,仍有較大差距。這將是未來很長一段時(shí)間內(nèi),制氫和推廣氫能也離不開傳統(tǒng)的煤炭和天然氣。無論是天然氣制氫還是煤制氫,經(jīng)過幾十年的發(fā)展,技術(shù)已經(jīng)相當(dāng)成熟,通過技術(shù)改進(jìn)降低成本的空間不大,成本構(gòu)成主要基于原材料價(jià)格受市場控制,波動性強(qiáng)。因此,雖然“灰氫”在中短期內(nèi)仍是氫能的主要來源,但無論是政策導(dǎo)向還是成本降低空間,未來氫能的可持續(xù)發(fā)展仍取決于“綠氫”由水電解產(chǎn)生。
電解水制氫成本應(yīng)從兩方面降低。一是降低電費(fèi)。由于目前我國工業(yè)用電成本仍居高不下,風(fēng)能、太陽能“棄電”制氫將是未來行業(yè)的主要發(fā)展方向。已經(jīng)有相關(guān)公司進(jìn)行嘗試;另一方面,要努力降低電解槽的采購成本,隨著堿性電解槽日趨成熟,需要重點(diǎn)對PEM電解槽進(jìn)行科技攻關(guān),努力降低制造成本,提高使用壽命,共同努力降低單邊制氫成本,努力降低天然氣或煤制氫的成本。
(2)盡快加大氫氣運(yùn)輸壓力,降低氫氣運(yùn)輸單位成本。在可預(yù)見的時(shí)期內(nèi),由于技術(shù)限制,使用長管拖車通過公路運(yùn)輸高壓氫氣是目前唯一的選擇。如上分析,如果國外氫氣運(yùn)輸壓力提高到50MPa,可運(yùn)輸氫氣3~4倍,降低單位運(yùn)輸成本(如運(yùn)輸距離為100公里時(shí),運(yùn)費(fèi)可降低了 75.3%),并且隨著運(yùn)輸距離的增加,高壓優(yōu)勢更加明顯。但目前國內(nèi)主流的氫氣壓縮管束以Ⅰ型瓶為主,不能承受20MPa以上的壓力,如果要達(dá)到 50 MPa,則需要裝載 III 型瓶或 IV 型瓶束。
目前,國內(nèi)有關(guān)部門尚未出臺相應(yīng)的高壓氫Ⅳ型鋼瓶標(biāo)準(zhǔn),面臨技術(shù)壁壘。國內(nèi)沒有企業(yè)可以生產(chǎn)IV型氣瓶,因此尚未實(shí)現(xiàn)商品化。III型瓶由于外層纏繞高強(qiáng)度碳纖維,主要依賴進(jìn)口,成本是I型瓶的數(shù)倍,主要用作燃料電池車載氫氣容器,尚未應(yīng)用于掛車管束。針對上述情況,一方面要加強(qiáng)科技開發(fā),努力實(shí)現(xiàn)關(guān)鍵材料國產(chǎn)化,降低III型和IV型瓶的生產(chǎn)成本;為瓶裝市場留出空間,放寬相關(guān)規(guī)定,加大氫運(yùn)輸對公路運(yùn)輸?shù)膲毫Α?/span>
(3)攻克“卡脖子”技術(shù),實(shí)現(xiàn)關(guān)鍵設(shè)備國產(chǎn)化。與傳統(tǒng)成品油產(chǎn)業(yè)鏈相比,加氫站成本占比遠(yuǎn)高于加油站。原因之一是加氫站的主要設(shè)備依賴進(jìn)口,增加了投資成本。以核心設(shè)備壓縮機(jī)為例,我國加氫站使用的壓縮機(jī)大多以進(jìn)口為主,國產(chǎn)壓縮機(jī)在關(guān)鍵指標(biāo)和系統(tǒng)可靠性方面還存在較大差距,僅此一項(xiàng)就占總投資的 30%以上,高于其他投資,除壓縮機(jī)外,車站儲氫鋼瓶、加氫機(jī)國產(chǎn)化程度略高,但在許多核心指標(biāo)上仍落后于國外產(chǎn)品,因此應(yīng)通過政策支持和鼓勵(lì),加大關(guān)鍵設(shè)備研發(fā)投入,力爭加氫站核心設(shè)備盡快國產(chǎn)化,降低投資成本。
(4)突破政策限制,實(shí)現(xiàn)現(xiàn)場制氫,從以上成本分析可以看出,運(yùn)輸成本占?xì)錃庹w成本的比重很大,解決這一問題的方法之一是分布式站制氫,即制氫加氫“零距離”。由于我國仍將氫氣列為危險(xiǎn)化學(xué)品,并要求在化工園區(qū)內(nèi)生產(chǎn),因此我國大部分加氫站均在站外供應(yīng)氫氣。因此,應(yīng)呼吁有關(guān)部門盡快將氫氣納入能源產(chǎn)品管理,有條件的地區(qū)優(yōu)先在加氫站制氫,利用小型化制氫裝置,如撬裝式天然氣制氫設(shè)備或光伏發(fā)電耦合電解水制氫,省掉運(yùn)輸成本,壓縮產(chǎn)業(yè)鏈長度,降低用氫成本。
(5)提高加氫站技術(shù)水平,優(yōu)化配置和技術(shù)創(chuàng)新。除了加氫站的建設(shè)和投資,日常管理和運(yùn)營水平也決定了氫氣的成本。目前,我國加氫站的穩(wěn)定性和可靠性與國外相比還有很大的提升空間,要實(shí)現(xiàn)連續(xù)運(yùn)行并保持穩(wěn)定的運(yùn)行條件,還需要進(jìn)行大量的改進(jìn)工作。研究表明,如果加氫站連續(xù)無故障加氫次數(shù)增加一倍,氫氣成本可降低1.5元/kg,如果每天加氫量增加15%,成本將降低1.0元/kg,如果電耗降低50%,氫氣將減少1.0元/kg。優(yōu)化加氫站配置,提高設(shè)備壽命,降低運(yùn)行能耗,提高可靠性。
其收益可能大于簡單建設(shè)成本的降低。
(6)提高儲氫設(shè)施利用率,由于氫氣的性質(zhì)和目前的技術(shù),無論是長管拖車的管束,還是加氫站的高壓瓶組,氫氣的利用率都只能達(dá)到70%~80%,造成巨大的損失和增加氫氣的成本。相關(guān)企業(yè)要加大科研開發(fā)力度,通過技術(shù)創(chuàng)新和工藝優(yōu)化,提高高壓氣瓶氫氣的利用率,減少損失,從而降低氫氣在運(yùn)輸過程和加氫站的成本。
隨著碳減排政策的不斷推進(jìn)、氫燃料電池汽車的大規(guī)模推廣以及氫能市場的逐漸成熟,市場對氫的需求將呈爆發(fā)式增長。雖然中短期內(nèi),傳統(tǒng)化石原料生產(chǎn)的“灰氫”仍將占據(jù)市場主導(dǎo)地位,但CCUS生產(chǎn)的“藍(lán)氫”和電解水結(jié)合可再生能源生產(chǎn)的“綠氫”將成為市場主流,未來的發(fā)展方向。雖然目前受制于高成本,氫能的推廣期必須依靠低價(jià)的“灰氫”,但隨著技術(shù)進(jìn)步和電價(jià)的降低,低碳?xì)涞氖袌龇蓊~將逐漸擴(kuò)大,占據(jù)主流市場。
同時(shí),通過技術(shù)創(chuàng)新和管理創(chuàng)新,疊加氫燃料電池汽車數(shù)量穩(wěn)步增加,產(chǎn)業(yè)配套設(shè)施逐步完善,達(dá)到一定臨界點(diǎn)后,氫的運(yùn)輸成本和建設(shè)運(yùn)營加氫站的成本將迅速降低,氫會變得更便宜,氫能產(chǎn)業(yè)將進(jìn)入快速擴(kuò)張階段。相信在政府的統(tǒng)一部署和大力推動下,通過相關(guān)科研單位、裝備制造企業(yè)、能源企業(yè)和燃料電池汽車企業(yè)的不斷努力與合作,氫能產(chǎn)業(yè)將很快通過目前的產(chǎn)業(yè)導(dǎo)入時(shí)期,逐步脫離政策支持,進(jìn)入實(shí)質(zhì)性工業(yè)化快速發(fā)展階段,我國“氫能社會”的目標(biāo)即將成為現(xiàn)實(shí)。
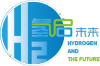